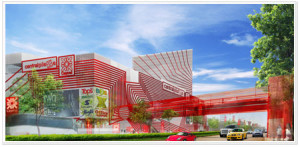
Central Changwattana Shopping Plaza buildings are designed to reduce energy consumption. The walls of building are mainly arranged in the North. Also, the environment is conducive to energy conservation by planting trees around the building to reduce the temperature of the surrounding buildings. The walls are designed with lower heat transfer to the walls and roofs to reduce the burden of the air conditioning system by using the glass areas is only 9.8 percent. Moreover, the buildings use the glass with low radiation (Low-E Glass). The colors of outside of the walls are light colors which benefits to the total heat transfer through the walls (OTTV) is 33.84 W/m2 better than the legal limit (not more than 40 W/m2)
Most of roof material about 94.4% is metal (Metal. Sheet) with covers by ceramic coating and contains inner insulation. Some areas of roof are designed by natural light (sky light) concept, which helps to reduce the overall heat transfer through the roof (RTTV) at 9.84 W/m2. This is better than the legal limit (not more than 10 W/m2). For the heat transfer prevention in the building, lightweight bricks are added between conditioned and non air-conditioned. Most electric light bulbs are compact fluorescent lamps of 26 W, fluorescent 18W and 36 W with electronic ballast, which can help to control turning off and on from centrally with Building Automation System (BAS).
Moreover, the buildings use natural daylight to reduce energy consumptions from the lights. Also, it can control the dimming light with natural light with Lux Sensor to adjust the suitable brightness. Air conditioning system is the cooling water system from the centrally by high efficiency of eight coolers with COP values between 0.55 – 0.67 kW/TR. Chiller Plant Management (CPM) can control cooling water flow rate and low temperature. Installation of Variable Speed Driver (VSD) with cold-water pumps and a cold wind transmitter can adjust the suitable speed to the load. In addition, the buildings installed intelligent elevator system, which can reduce energy consumption over 10% when compared to typical elevator.
The energy management system in the buildings is used BAS system to help in the planning and monitoring of energy consumption data, maintenance, and controlling of major equipment. Moreover, the buildings implement energy conservation measures under the law. The working group was set up to conduct activities on energy conservation of energy policy of the executive boards and as required by law. Furthermore, the building has environmental management as well as waste water treatment follow the standard such as rain catchment system, condensate water from air cooling for watering plants, and cooling tower.
Savings Narrative
The buildings are constructed in 2007 by focusing on the energy-saving benefits, modernization and safety. Materials are selected by the standards of the construction and friendly with environmental as following:
- Air Conditioning System
The building is equipped with a high-efficiency chiller, which uses low-flow low-temperature technology, controlled through a CPM (Chiller Plant Management) system and monitored in real-time, with the ability to refer to past operational data such as set-point
adjustments, chiller flow tests of each run, and water temperatures in the heat ventilation. Besides the chiller, other equipment such as the chilled water pump (CHP), condensate water pump (CDP) and cooling tower (CT) can also be controlled and monitored systematically.
The system incorporates VPF (Variable Primary Flow). The chilled water pump (CHP) is installed with a VSD (Variable Speed Drive), which allows the speed to be adjusted to match the actual load.
The air handling unit (AHU) also has a VSD to control temperature, humidity and indoor air quality at appropriate levels, set through an IBMS (Intelligent Building Management
System) for ease of management and adjustment to different climates and seasons.
In addition to smart design, equipment selection and performance capabilities, managing
the operation of the water chiller is also important. The facility has operated the water
chiller and related equipment at maximum efficiency, thereby reducing the amount of
equipment that needed to be installed. The building use high efficient chiller which yield
better energy performance rate (kW/TR) conventional type and save energy of approximately 1,800,000 kWh/yr.
- Lighting System All lighting systems installed within the shopping complex utilize energy-saving fixtures and devices, such as 26 Watt compact fluorescent lamp and 18/36W fluorescent bulbs with electronic ballasts, which are controlled throughout the shopping complex, parking building and around the complex as follows:
- Lights within and around the shopping complex and inside the parking building are
turned on and off at scheduled times through the IBMS.
- Some fixtures are controlled in relation to natural sun light. For example, the cove lights around theinterior skylights are operated via lux sensors that monitor the light in the space and signal a dimmer to adjust the lamp brightness to an average as required (min. 200 lux), and close to optimal (at 250 lux) using electric power installed per area equal to 11.5 W/m2.
- Photodetector cells are installed to control lighting within the parking area and around the outside of the shopping complex building.
- The lighting system is subdivided into small sub-circuits for ease of use and control. Separate switches are incorporated for circuits controlled by natural light levels, distinct from conventional circuits for both indoor and outdoor lighting.
- Energy-saving LEDs are used for nighttime exterior lighting, instead of conventional floodlights which consume electricity at a much higher rate.
- Other Systems
- A Deep Shaft Wastewater treatment system is used for space savings and lower system installation costs than typical systems. The water quality after treatment is at an acceptable level, and better than standard. A water reuse system incorporates treated wastewater for secondary uses, such as watering plants and cleaning the pavement outside the shopping complex.
- The freight lifts of the shopping complex use a technology called “Intelligent Lift”, an elevator control system that has the following features:
A) Intelligent Traffic Planning (Zoning) is optimized for the actual use of the building, which helps reduce problems during times of extreme traffic.
B) The Destination Control System can combine passengers going to the same floor or zone, which makes travel fast, and reduces energy use. The advantages of using the Intelligent Lift are:
- Reducing travel time as compared to normal passenger lifts.
- Reducing the number of lifts needed,resulting in initial cost reduction.
- Using about 10% less energy than normal lifts.
- Reducing passenger congestion in front of the lift halls and within each lift.
Indoor Air Quality
The indoor air quality within the shopping complex is around 25-26°C, relative humidity not exceeding 50.5% RH (data from room temperature sensor within the AHU room),with an air ventilation rate of 20 m3/hr/person. There is also a CO2 sensor to control the air quality.
Overall Energy Consumption Per Air-Conditioned Area (kWh/m2-yr.)
The air-conditioned areas within the shopping complex of about 108,162 m2 are central public areas and spaces leased by tenants. Electrical energy consumption per air conditioned area is calculated to be 207.4 kWh/m2-yr.